The Victoire made for the Concours de Machines 2019 (Paris-Brest-Paris)
Once again, the Victoire team decided to join the "Concours De Machines" 2019. This year, the rules were written by the magazine 200, in the form of a letter from a certain "Mr Dreamer" describing the fantasies of a long-distance regular, searching for a new bicycle. Here is our proposal, as per the wishes of Mr Dreamer, which allowed us to win the Concours de Machines 2019.
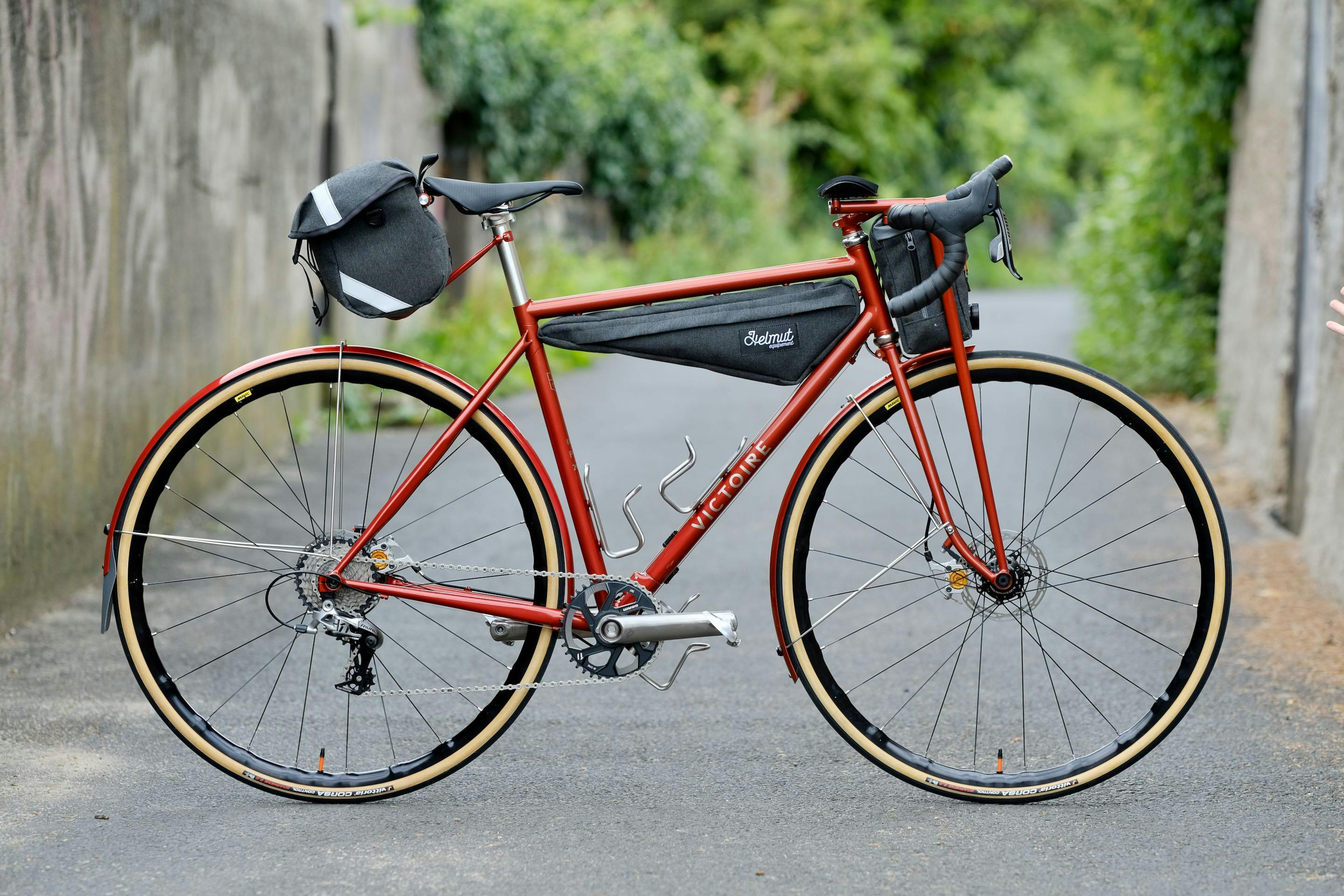
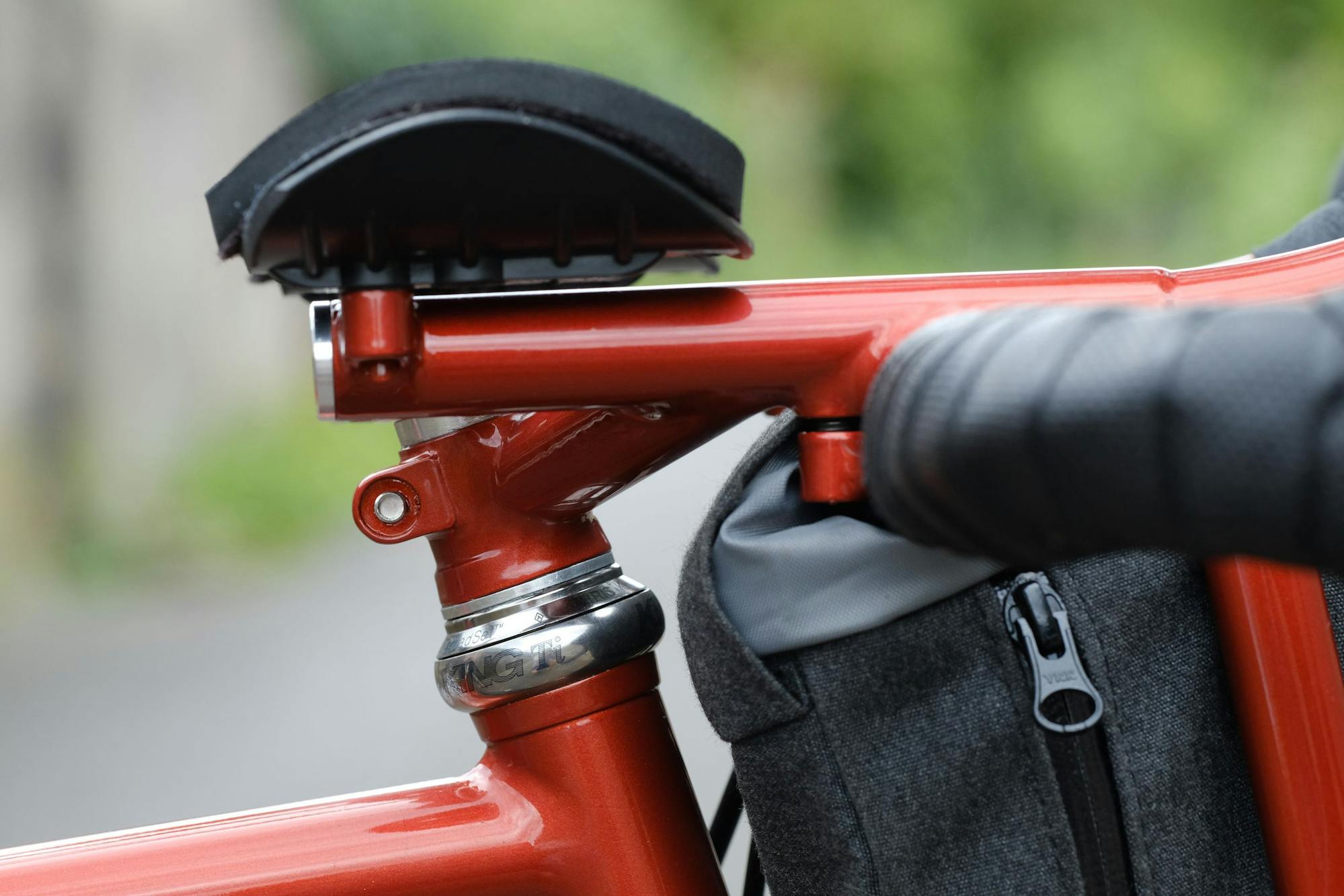
While brainstorming in February, several things became obvious to us: the bike built for this contest would not only be a model to show our know-how, but it would also be a field of exploration, a prototype allowing us to get out of our comfort zone and test new ideas. Finally, it would be a bike that we will keep in our showroom, like the models created for previous editions.
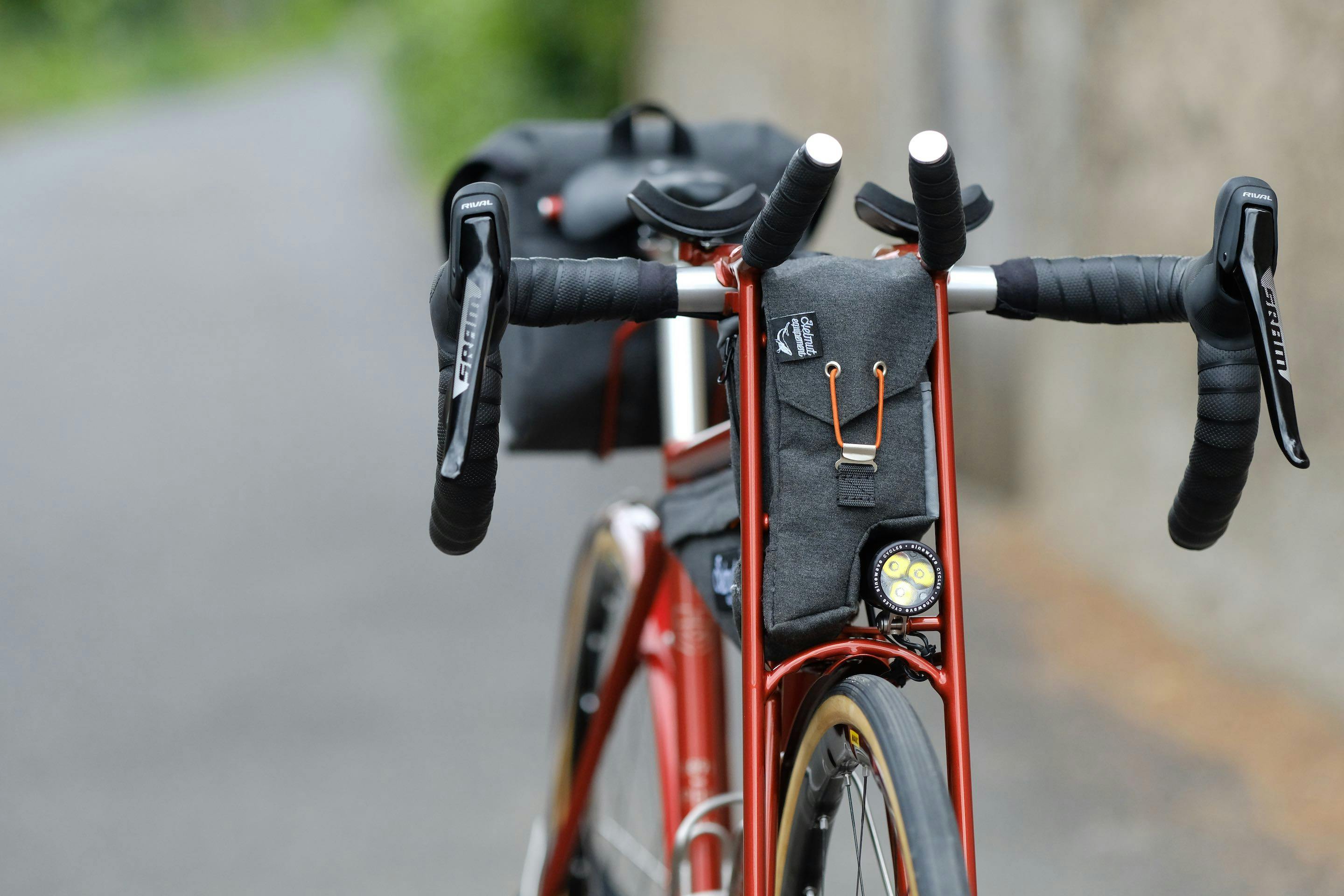
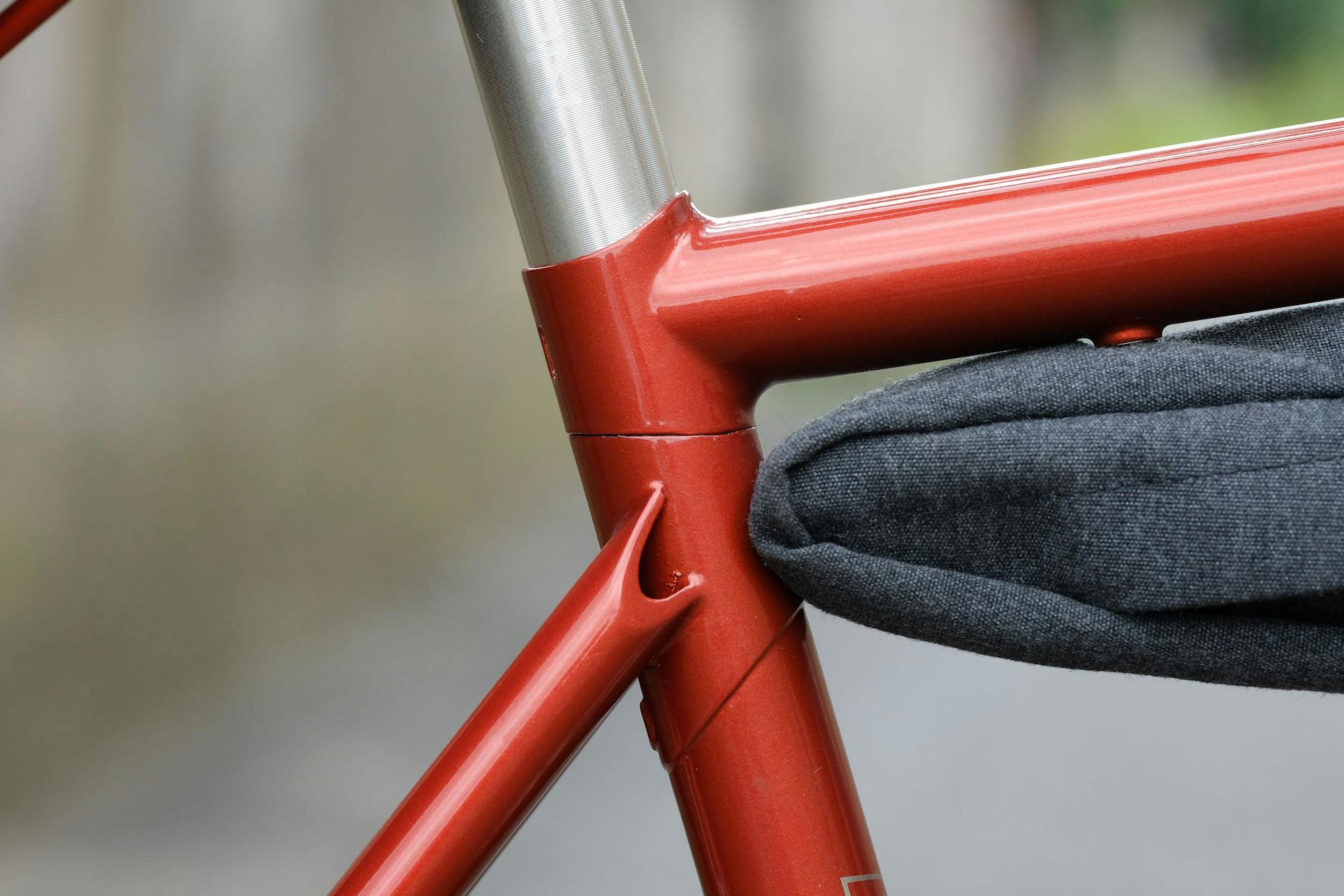
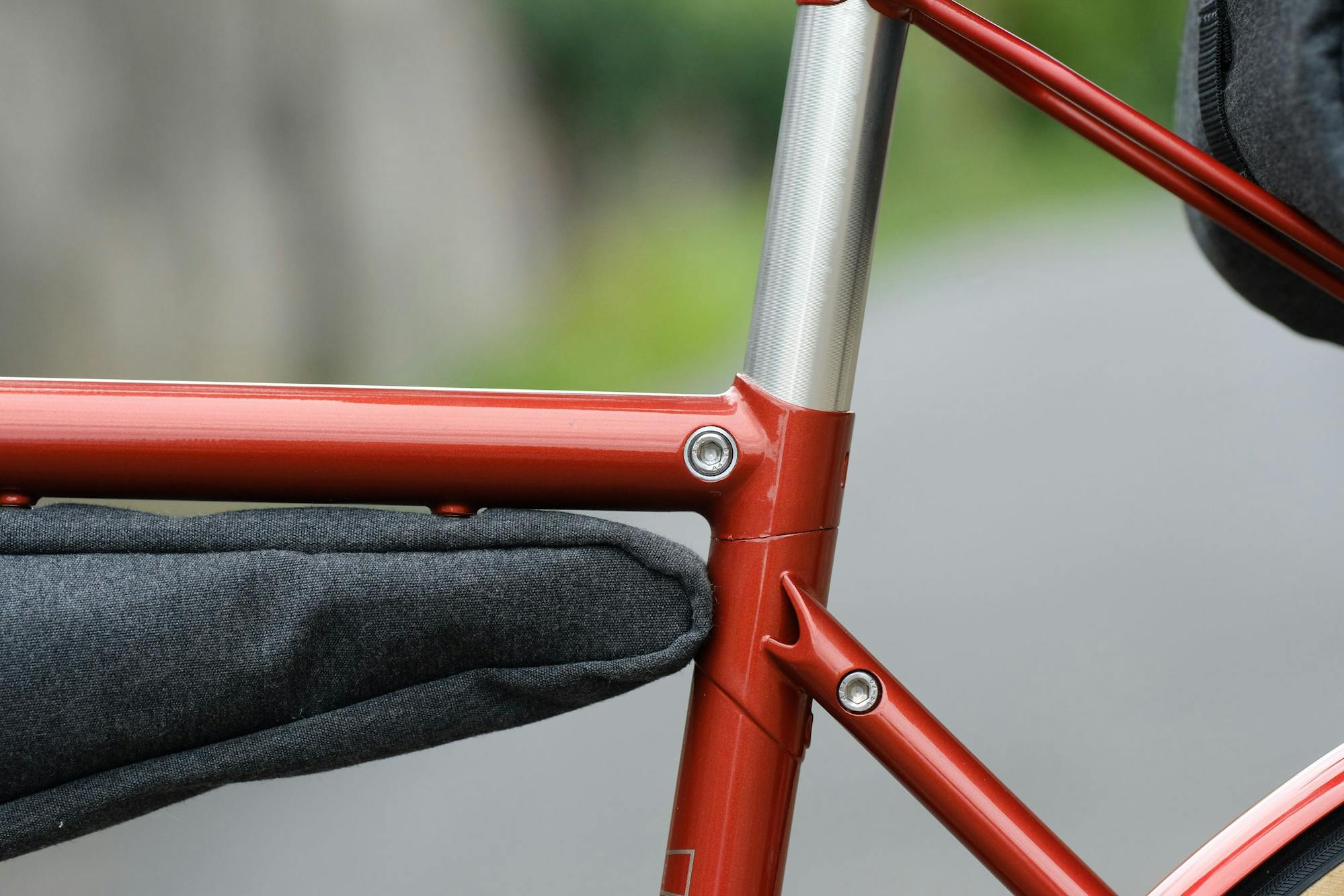
Reading Mr Dreamer''s letter revealed an important point: the frame had to be built for travel (breaks into two pieces). We had already offered a machine of this type in 2017. The concept combining Break-away system invented by Ritchey and a S&S coupler had many advantages, but also the main disadvantage of having to carry a specific key. We quickly agreed to start from scratch, while making sure that the bike could be fully taken apart with just a 5mm Allen key. To achieve this, we designed our own CAD coupler system. Manufacturing was then outsourced to a local company, Add-Up.
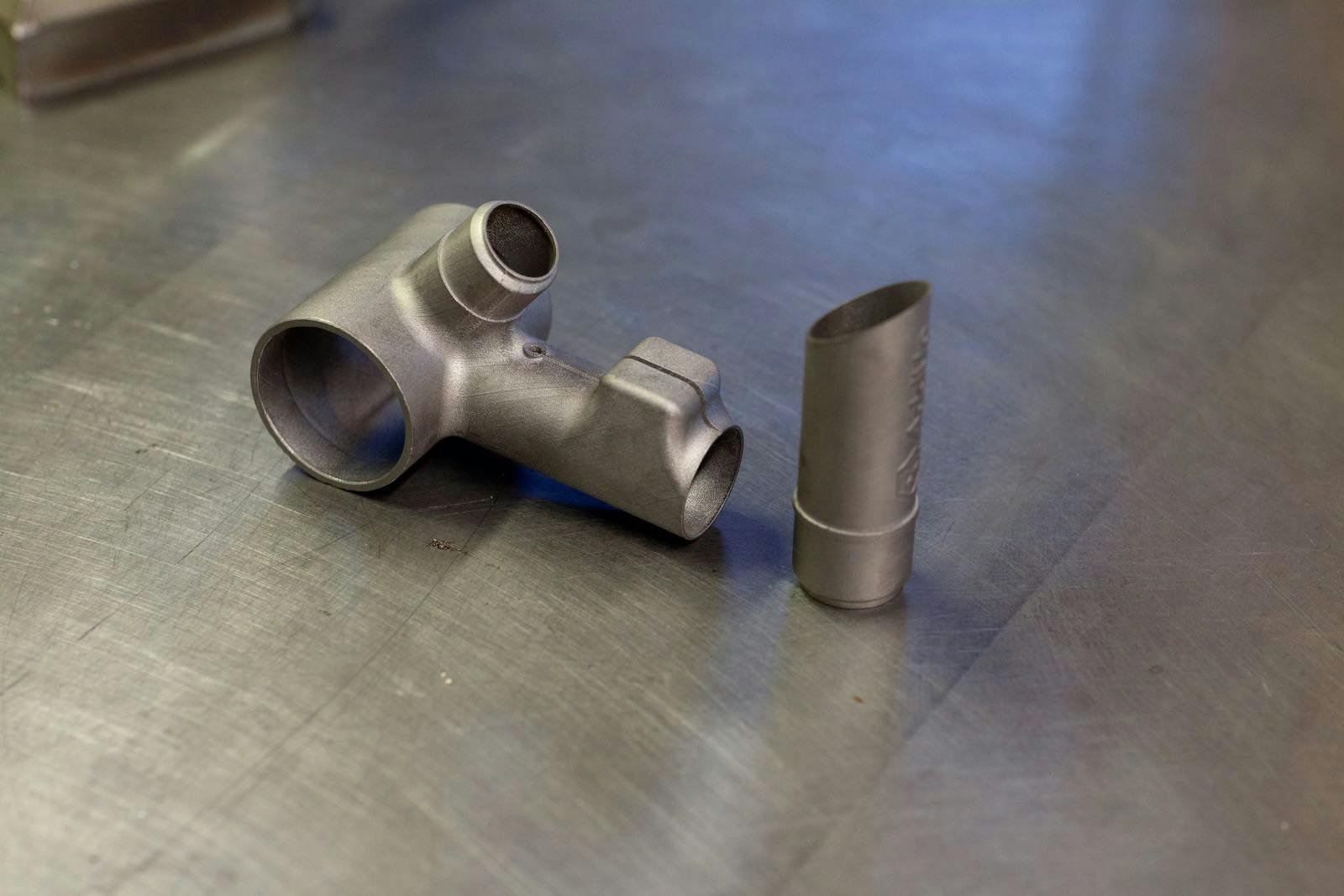
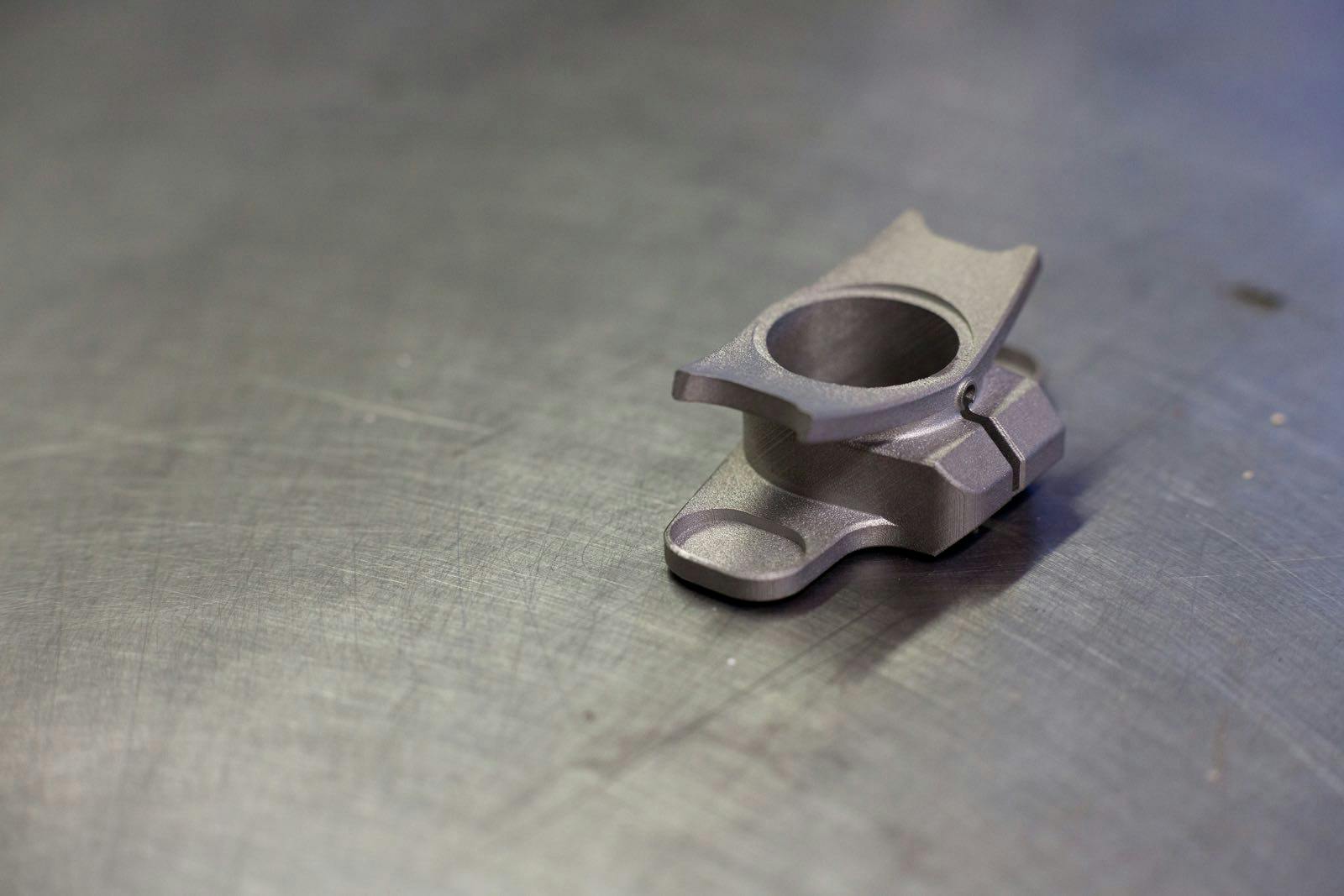
Add-Up, a subsidiary of Michelin, specializes in additive manufacturing. Recent and innovative, additive manufacturing can be likened to 3D printing, but here, the technology makes micro-welds of metal dust, in order to create a part layer by layer. Add-Up, which is both a pioneer and market leader in the field, makes it possible to manufacture unique, extremely resistant parts, with mechanical characteristics superior to parts obtained by molding (such as frame connector parts). We therefore designed five parts which were manufactured in Clermont-Ferrand from Maraging steel (an alloy used among other things to manufacture the 953 stainless steel tubes at Reynolds). These parts substitute for a coupler or break-away system, while having the benefit of being manufactured locally. The Add-Up factory is actually located just a few kilometers from our workshop.
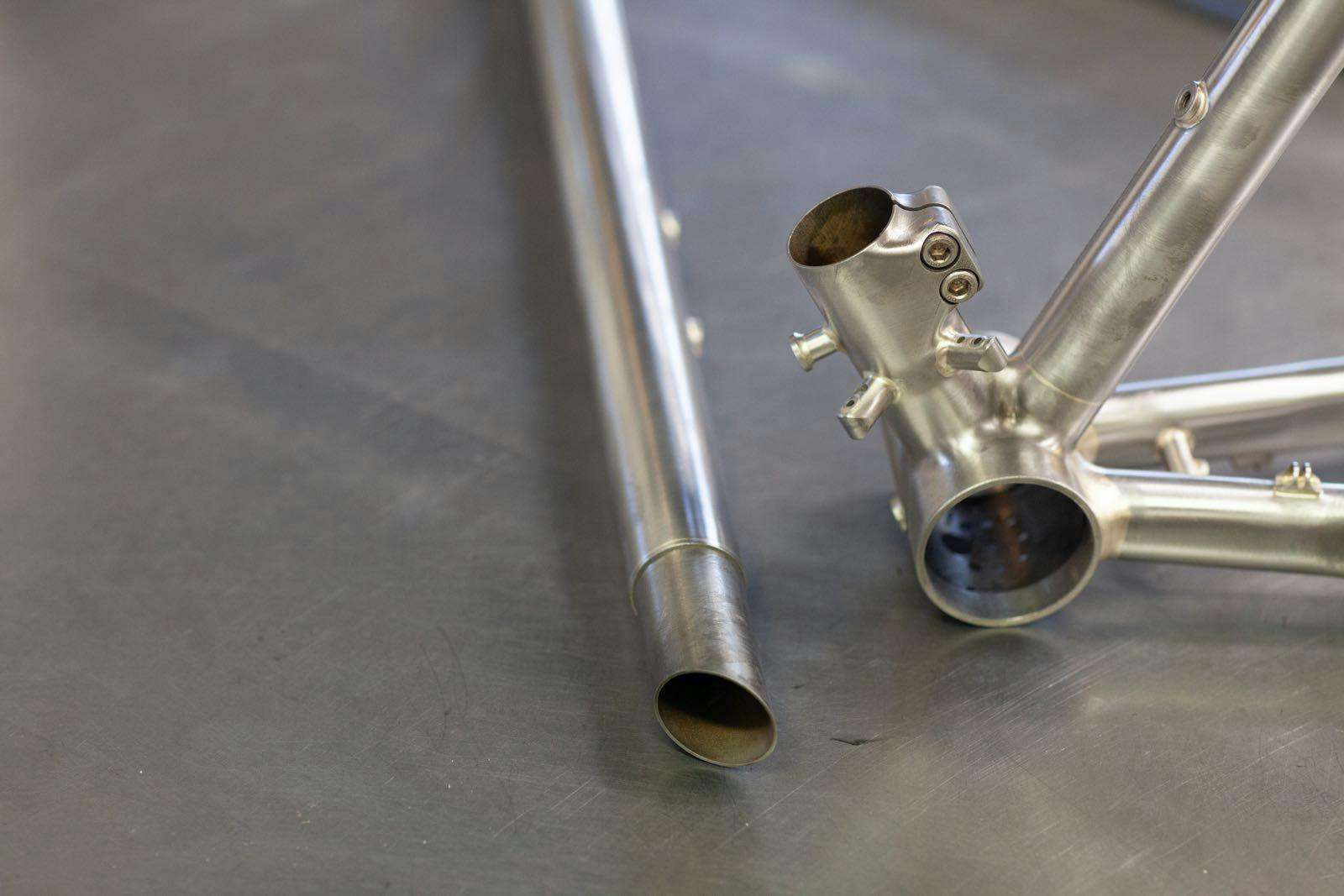
Proud of our know-how, we then produced the frame in a completely traditional way, with notches and hand-polished welds. All the frame and fork tubes come from our Italian friends : Columbus. Olivier was responsible for the manufacture of the frame, while Luka looked into the huge challenge of the fork unit.
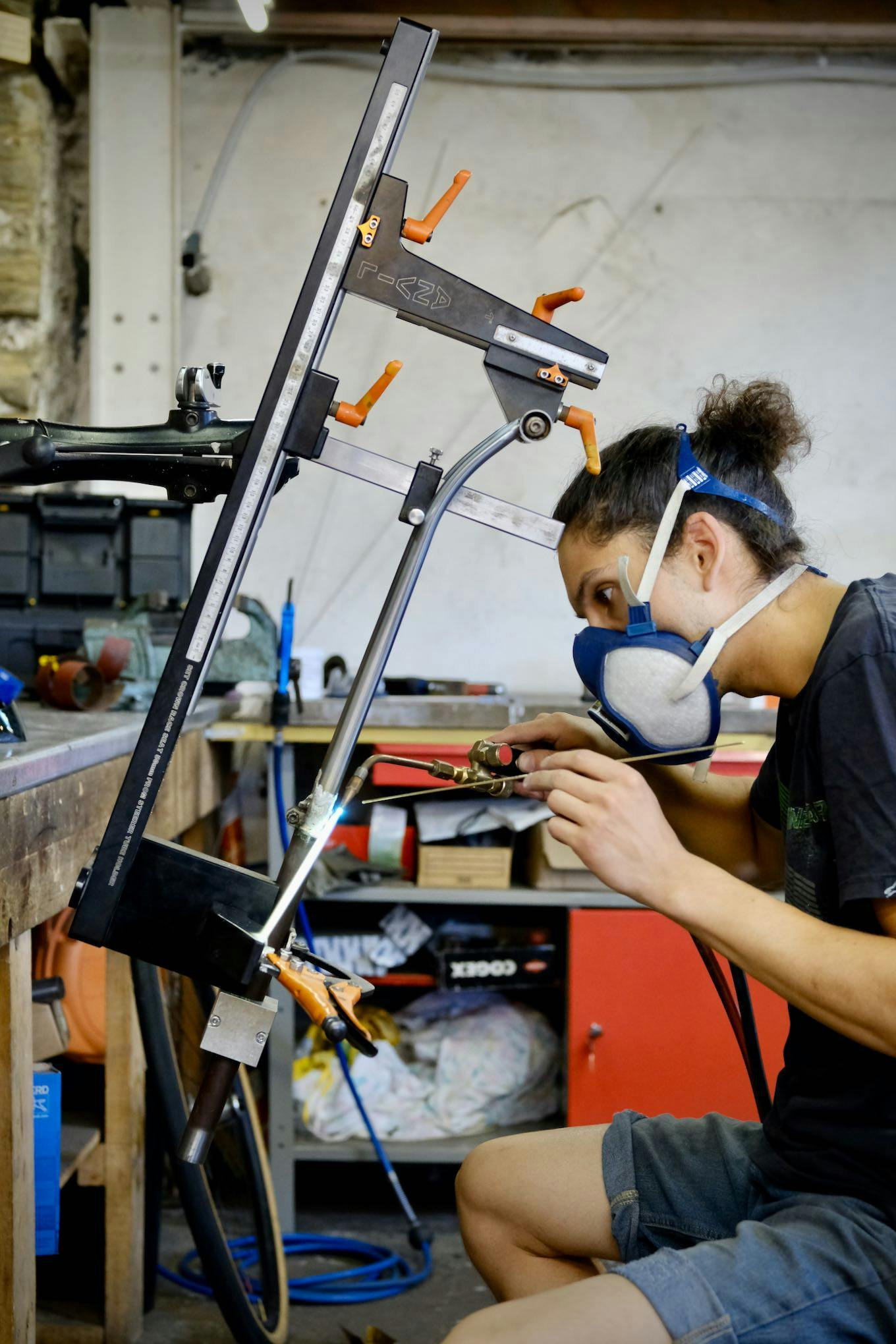
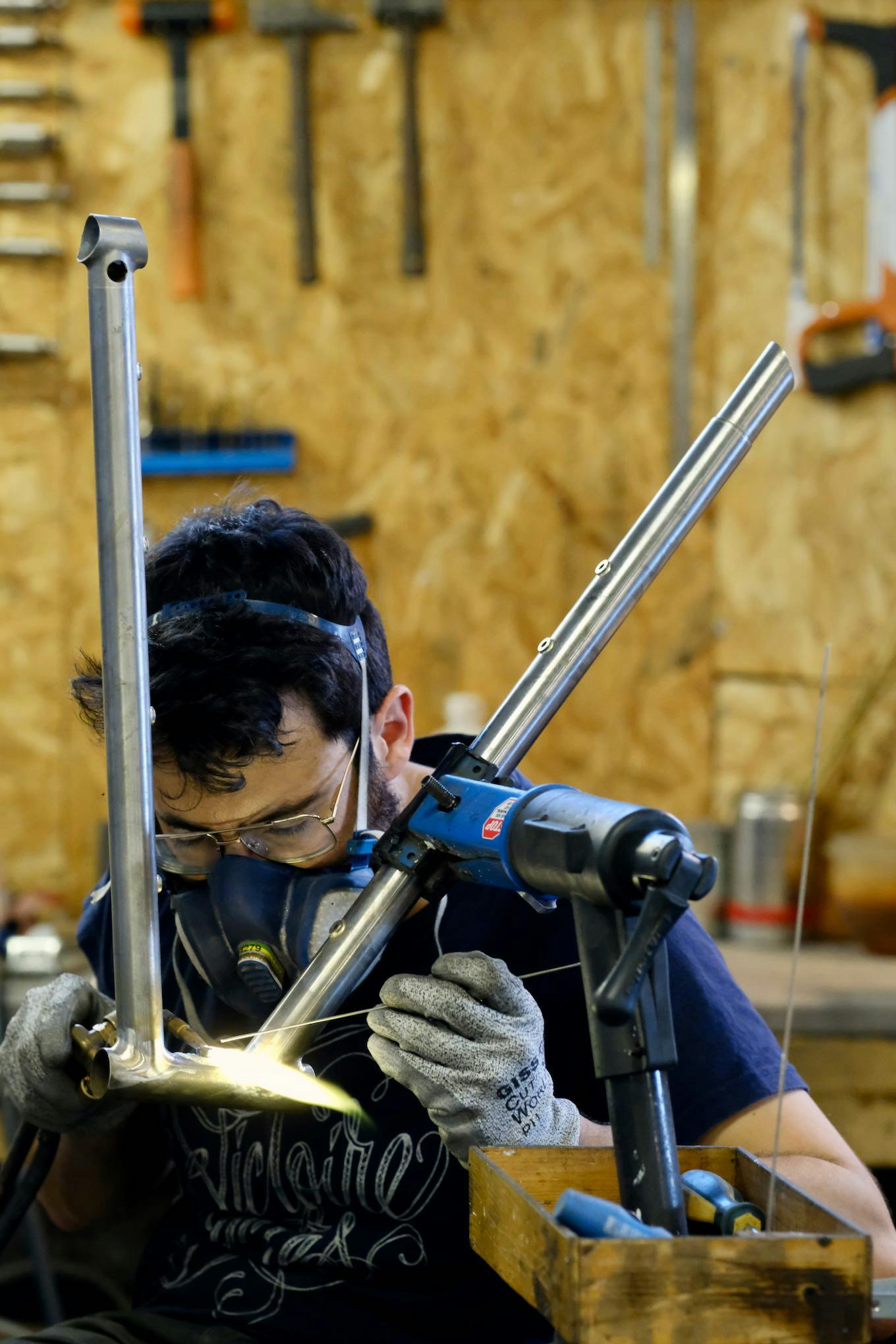
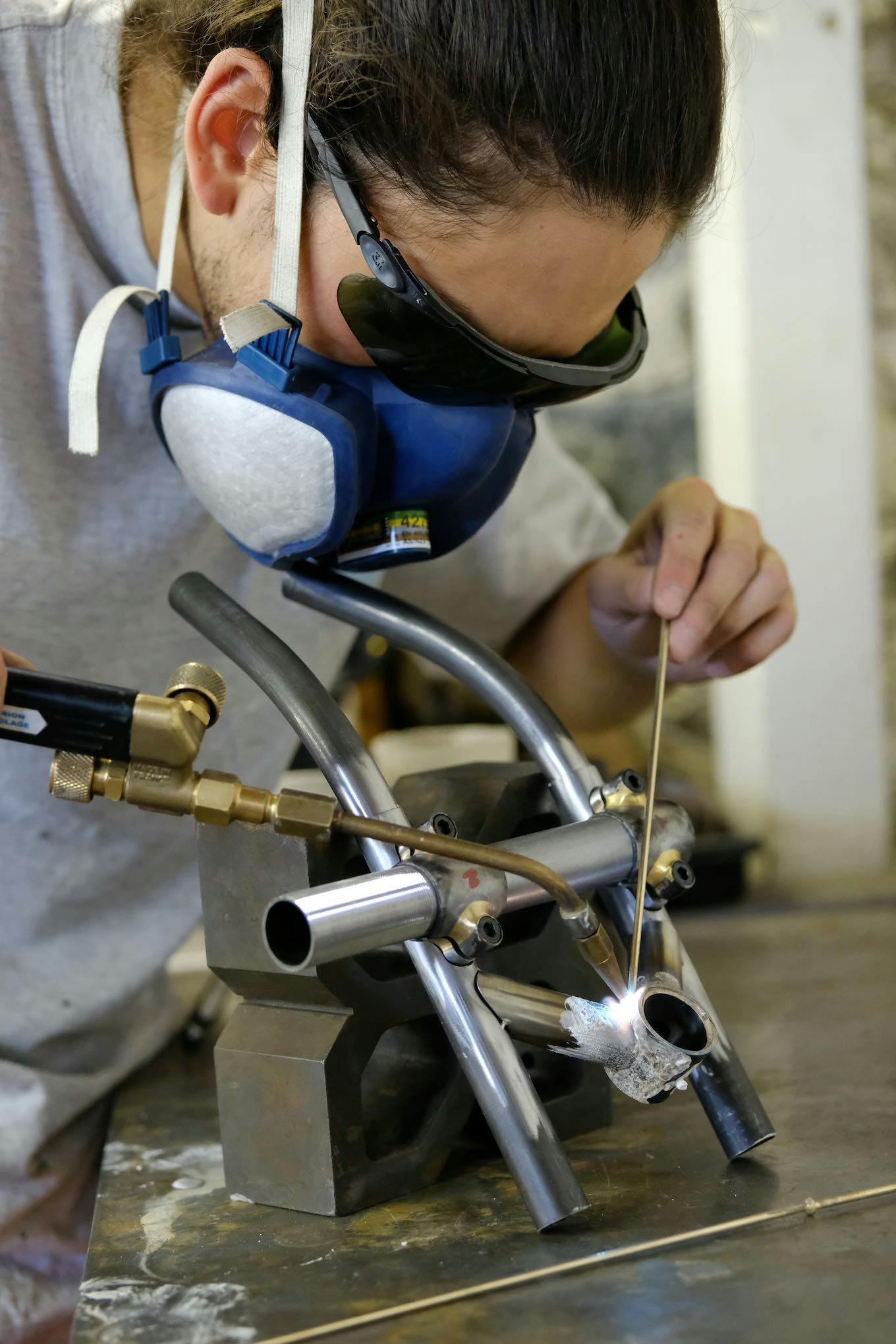

The second area of concern was the numbness in the hands typically experienced following 90 hours of holding onto the handlebars. The classic solution is to use triathlon handlebar extensions, which are raised to obtain a comfortable position. But this solution has the disadvantage of being unattractive visually, and it adds weight to the whole bike. Our thinking starts from a simple observation: on a modern long-distance bike with extensions, the front end looks very busy, with a multitude of tubes and bags. We therefore tried to reduce the number of tubes by assigning them a maximum number of functions, according to the "less is more" principle, dear to Ludwig Mies Van Der Rohe.
The result is a 100% unique piece, having the functions of fork, stem, arms extension and luggage rack at the same time.
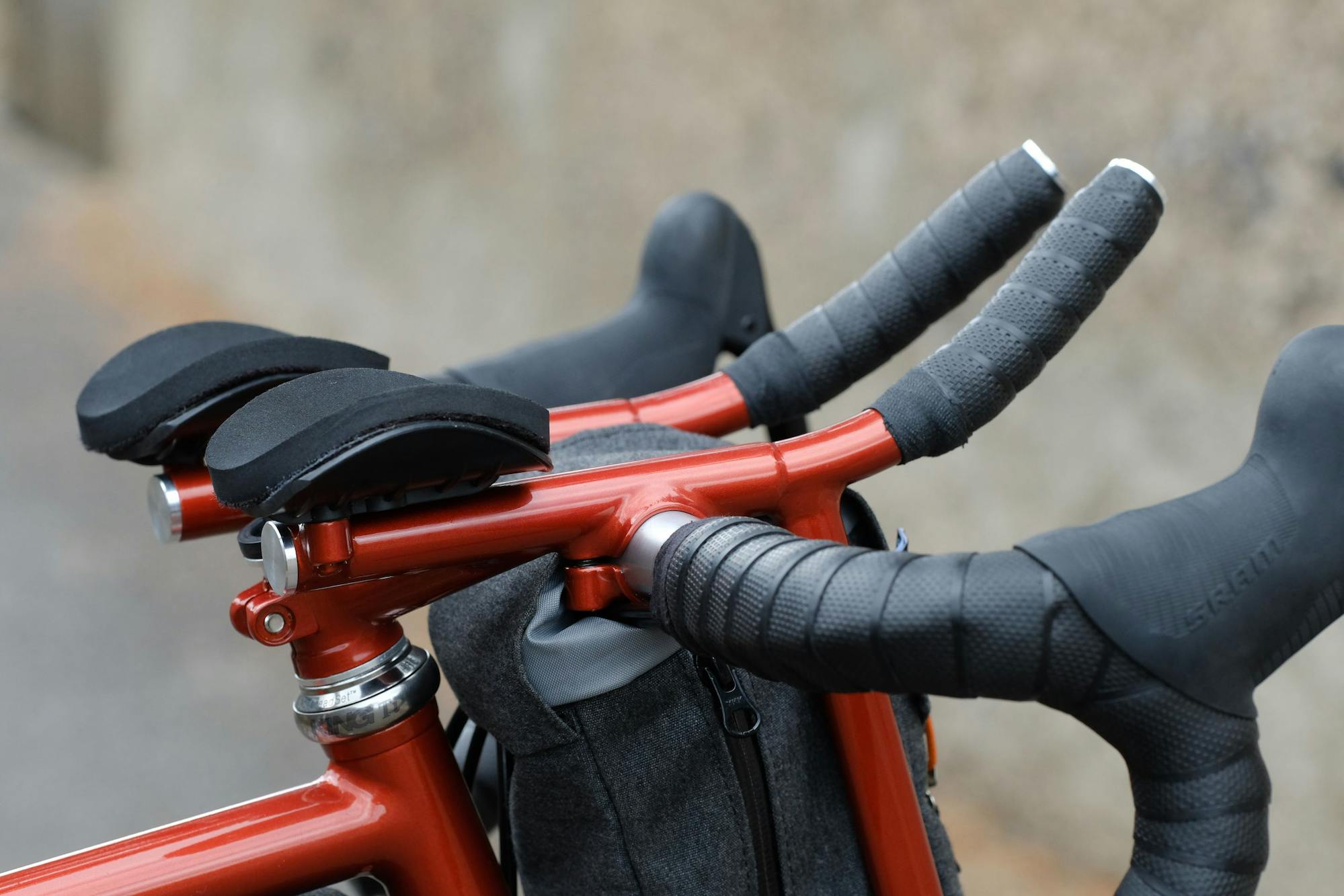
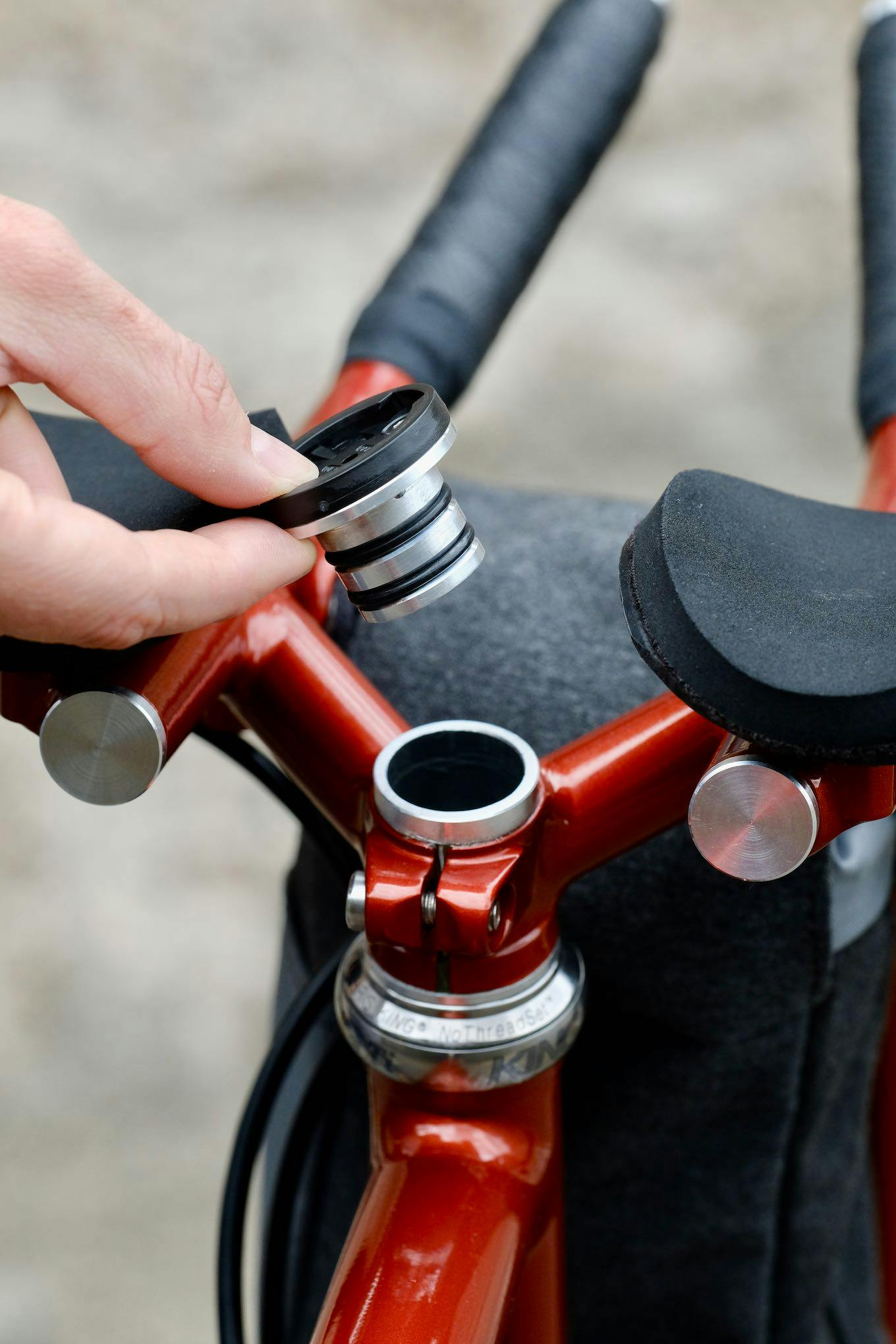
We have also added a personal challenge for this year: reduce the use of plastic parts to the strict minimum, and ban carbon completely. Our project is thus made up of recyclable materials, and we have favored parts that are robust and easy to repair. To save weight, we designed and manufactured as many components as possible, such as the GPS mount built into the stem cover, and anything that could not be manufactured in the workshop has been modified where possible.
The production of the frame for the Concours de Machines 2019 took two weeks and required around 50 hours of work by two frame builders. Despite the presence of parts in additive manufacturing, many small parts and details had to be produced in the traditional way. The frame, made of Columbus Life tubes, weighs the same as a conventional frame, even with the in-house coupler system. All the small brazed parts are made of stainless steel, so as to eliminate any possible corrosion. To add to the bike's uniqueness, the steerer tube is 1'' in diameter, despite the disc braking system. This saves a significant amount of weight on the front of the bike and this gain is only possible thanks to the particular design of the fork.
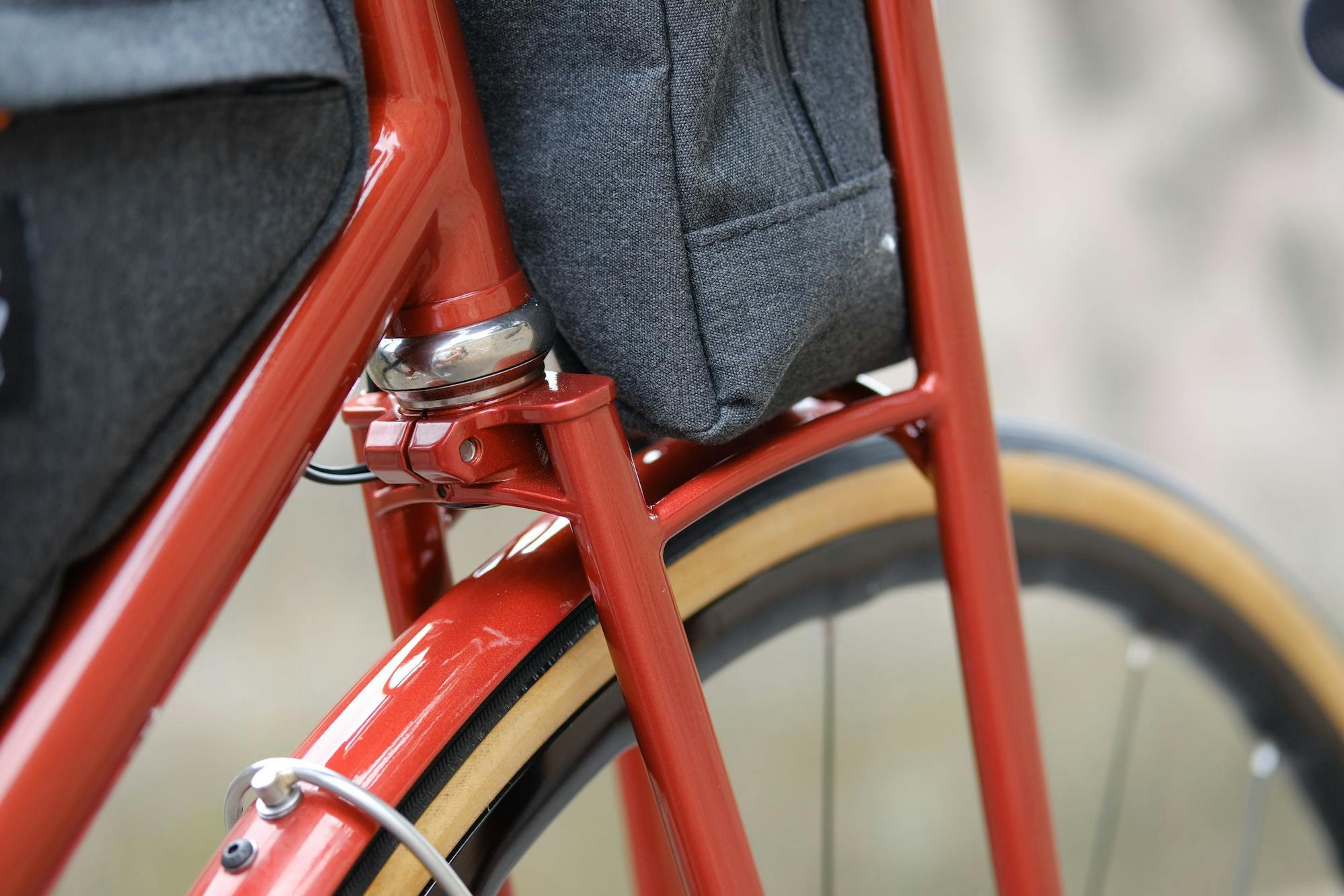
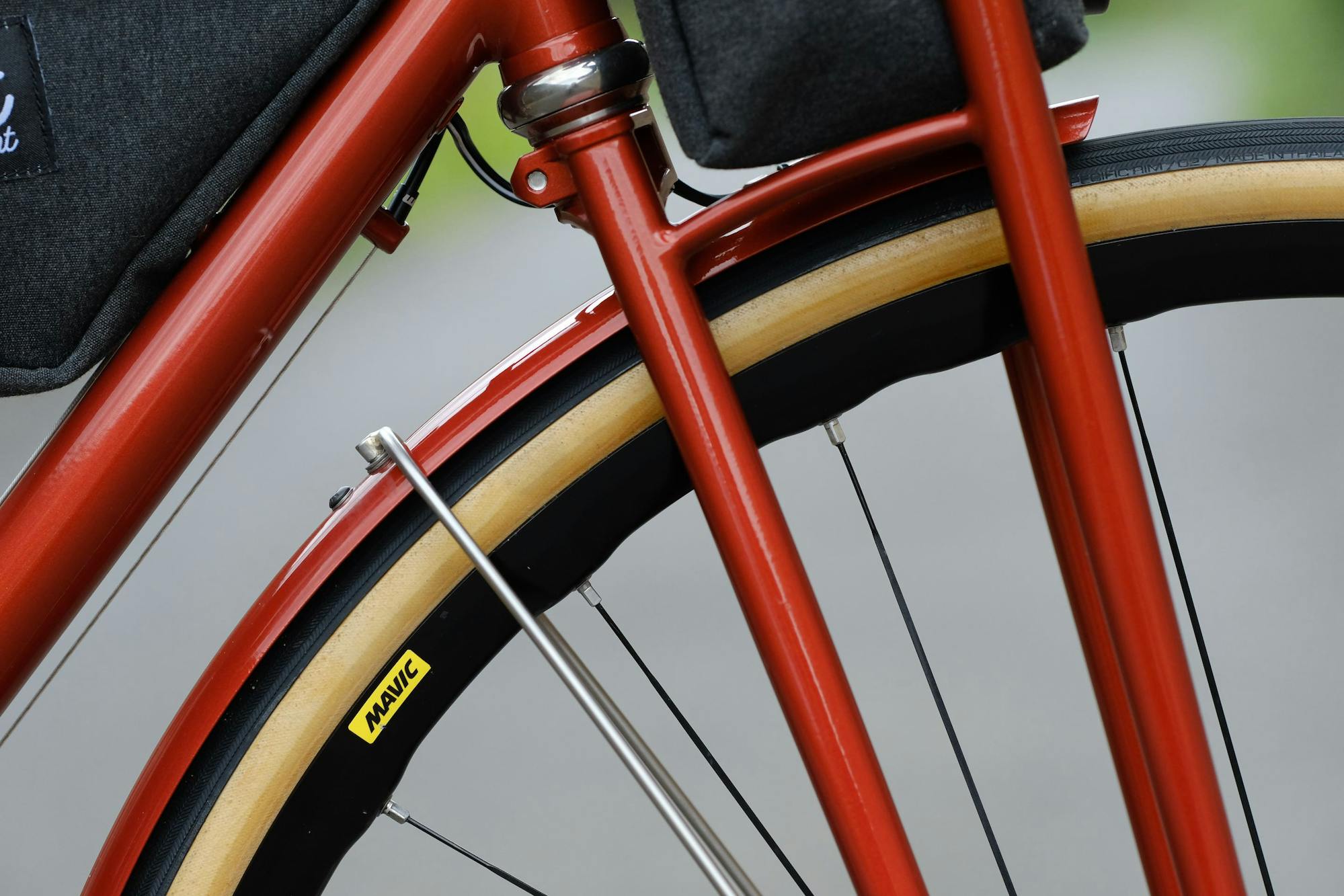
The fork took almost as long as the frame to be manufactured. No less than 45 hours of work were necessary to manufacture this assembly regrouping multiple functions. The main concept here was to condense the fork, the stem, the extensions and the luggage rack into a single piece. This integration technique made it possible to save weight, while remaining on a structure made 100% in Columbus steel in the workshop. We were thus able to gain 400 grams with our integrated fork unit, compared to a set of carbon fork, rack, stem and aluminum extensions, while refining the lines of the bike.